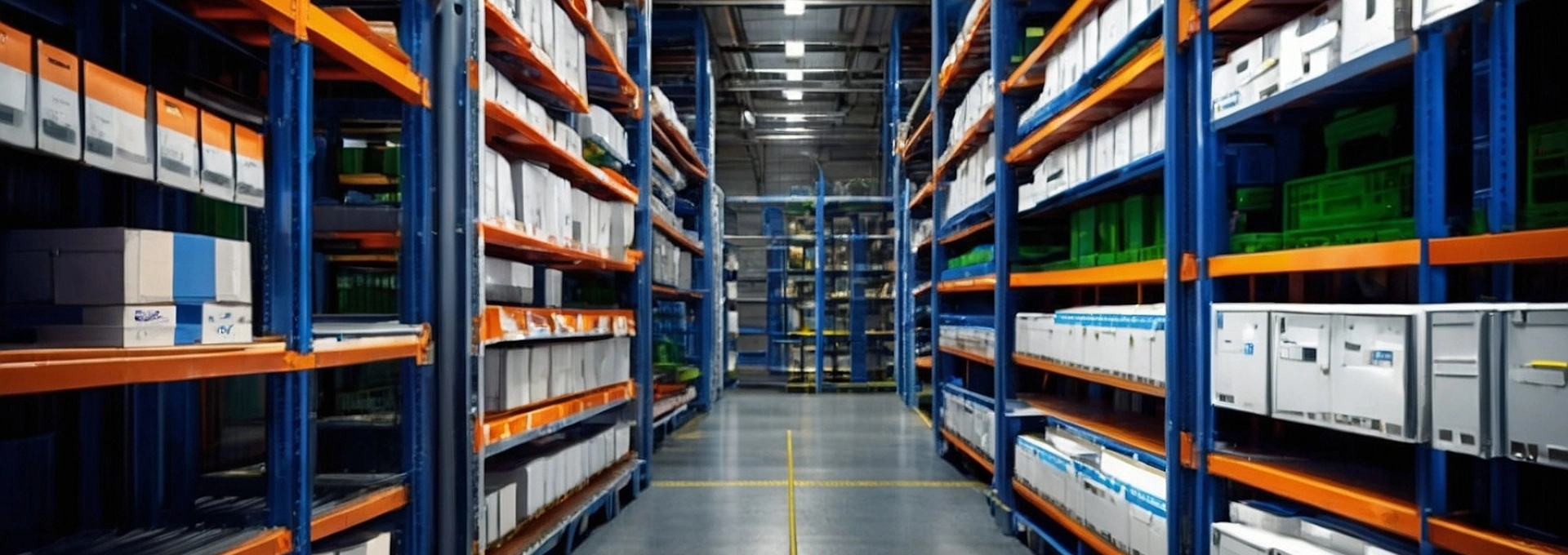
L'optimisation logistique est devenue un enjeu majeur pour les entreprises cherchant à améliorer leur compétitivité. Au cœur de cette optimisation se trouvent les systèmes de stockage, dont les racks industriels constituent un élément clé. Ces structures métalliques robustes permettent de maximiser l'utilisation de l'espace vertical, d'organiser efficacement les marchandises et de faciliter les opérations de manutention. Avec l'évolution rapide des technologies et des pratiques logistiques, il est crucial de comprendre les différentes options disponibles et leurs applications spécifiques pour faire le choix le plus judicieux.
Types de racks de stockage industriels et leurs applications spécifiques
Les racks de stockage industriels se déclinent en plusieurs catégories, chacune adaptée à des besoins logistiques particuliers. Le choix du système approprié dépend de facteurs tels que la nature des produits stockés, la fréquence de rotation des stocks et les contraintes spatiales de l'entrepôt.
Les racks à palettes conventionnels sont les plus répandus. Ils offrent un accès direct à chaque palette, facilitant ainsi la gestion des stocks selon le principe du first-in, first-out (FIFO). Ces structures sont idéales pour les entrepôts gérant une grande variété de références avec des rotations fréquentes.
Pour les entreprises confrontées à des contraintes d'espace, les racks à accumulation (ou drive-in) permettent de stocker un grand nombre de palettes en profondeur. Cette solution est particulièrement adaptée aux produits homogènes avec une rotation plus lente, fonctionnant sur le principe du last-in, first-out (LIFO).
Les racks cantilever, caractérisés par leurs bras en porte-à-faux, sont conçus pour le stockage de charges longues et encombrantes telles que les tuyaux, les profilés métalliques ou les planches de bois. Ils offrent une flexibilité incomparable pour les matériaux de formes irrégulières.
Les racks dynamiques, équipés de rouleaux inclinés, facilitent la rotation naturelle des stocks. Les palettes sont chargées d'un côté et se déplacent par gravité vers le côté de déchargement, assurant une gestion FIFO optimale. Cette solution est particulièrement prisée dans l'industrie agroalimentaire ou pharmaceutique, où la gestion des dates de péremption est cruciale.
Critères de sélection et dimensionnement des systèmes de rayonnage
Le choix d'un système de rayonnage adapté nécessite une analyse approfondie de plusieurs paramètres. Une approche méthodique permet de garantir non seulement l'efficacité opérationnelle, mais aussi la sécurité et la conformité aux normes en vigueur.
Analyse des flux logistiques et rotation des stocks
L'étude des flux logistiques est primordiale pour déterminer le type de rack le plus approprié. Il convient d'examiner la fréquence des entrées et sorties, le volume de marchandises traitées quotidiennement, et les pics d'activité saisonniers. Une rotation rapide des stocks justifiera l'investissement dans des systèmes dynamiques, tandis qu'une rotation plus lente pourrait s'accommoder de solutions statiques moins coûteuses.
La méthode ABC d'analyse des stocks peut s'avérer précieuse dans ce contexte. Elle consiste à classer les produits en trois catégories selon leur importance en termes de valeur ou de fréquence de manipulation. Les produits A, les plus critiques, doivent bénéficier d'un accès rapide et facile, tandis que les produits C peuvent être stockés dans des zones moins accessibles.
Calcul de la capacité de charge et résistance structurelle
Le dimensionnement des racks doit prendre en compte le poids maximal des unités de charge, qu'il s'agisse de palettes, de conteneurs ou de caisses. La capacité de charge doit être calculée non seulement pour chaque niveau, mais aussi pour l'ensemble de la structure. Il est crucial de ne pas sous-estimer ces valeurs pour éviter tout risque d'effondrement.
Les ingénieurs utilisent des logiciels de calcul spécialisés pour déterminer la résistance des poutres et des montants en fonction des charges prévues. Ces calculs prennent en compte les normes de sécurité telles que l'EN 15512
pour les tolérances, déformations et jeux.
Conformité aux normes de sécurité et réglementations
La conception et l'installation des racks de stockage sont soumises à des réglementations strictes visant à garantir la sécurité des opérateurs et l'intégrité des marchandises. En Europe, la norme EN 15635
définit les directives pour l'utilisation et l'inspection des systèmes de stockage.
Il est impératif de respecter ces normes, non seulement pour des raisons légales, mais aussi pour optimiser la durée de vie des installations et minimiser les risques d'accidents. Cela implique la mise en place de protections contre les chocs, de systèmes anti-chute et de signalétiques appropriées.
Intégration avec les systèmes de manutention automatisés
L'avènement de l'industrie 4.0 a conduit à une intégration croissante des systèmes de stockage avec des solutions de manutention automatisées. Les racks doivent donc être conçus en tenant compte des spécificités des engins de manutention utilisés, qu'il s'agisse de chariots élévateurs automatisés (AGV) ou de transtockeurs.
Cette intégration nécessite une précision accrue dans le positionnement des racks et peut influencer le choix des matériaux utilisés. Par exemple, l'utilisation de guidages au sol ou de rails de guidage pour les transtockeurs impose des contraintes spécifiques sur la conception des allées et la structure des racks.
Technologies avancées pour l'optimisation du stockage vertical
L'optimisation du stockage vertical représente un levier majeur pour accroître la capacité de stockage sans augmenter la surface au sol. Les technologies modernes offrent des solutions innovantes permettant d'exploiter pleinement la hauteur disponible dans les entrepôts.
Systèmes de stockage dynamique à gravité
Les systèmes de stockage dynamique à gravité constituent une évolution significative des racks conventionnels. Ces structures utilisent la force de gravité pour déplacer les palettes ou les conteneurs d'un point de chargement vers un point de prélèvement, généralement sur des plans inclinés équipés de rouleaux.
L'efficacité de ces systèmes repose sur leur capacité à optimiser la rotation des stocks selon le principe FIFO. Ils réduisent considérablement les déplacements des opérateurs et des engins de manutention, contribuant ainsi à une meilleure productivité. Selon des études récentes, l'utilisation de systèmes dynamiques peut réduire jusqu'à 40% le temps nécessaire aux opérations de picking.
Racks mobiles sur rails pour maximiser l'espace
Les racks mobiles sur rails représentent une solution ingénieuse pour les entrepôts confrontés à des contraintes d'espace. Ces systèmes consistent en des rangées de racks montées sur des bases mobiles, se déplaçant sur des rails au sol. En éliminant le besoin d'allées fixes entre chaque rangée, ils permettent d'augmenter considérablement la capacité de stockage.
Cette technologie est particulièrement adaptée aux entrepôts frigorifiques ou aux archives, où le coût au mètre carré est élevé. Des études de cas ont montré que l'implémentation de racks mobiles peut augmenter la capacité de stockage jusqu'à 80% par rapport à des systèmes fixes traditionnels.
Solutions de stockage à navettes automatisées
Les systèmes de stockage à navettes automatisées représentent l'avant-garde de l'automatisation dans les entrepôts modernes. Ces solutions utilisent des navettes autonomes qui se déplacent à l'intérieur des structures de rayonnage pour déposer et récupérer les palettes.
L'avantage principal de ces systèmes réside dans leur capacité à exploiter des profondeurs de stockage importantes tout en maintenant un accès rapide aux marchandises. Ils sont particulièrement efficaces pour la gestion de grands volumes de produits homogènes. Des statistiques récentes indiquent que les entrepôts utilisant des navettes automatisées peuvent traiter jusqu'à 300 palettes par heure, soit une augmentation de la productivité de l'ordre de 25% par rapport aux systèmes conventionnels.
Gestion informatisée et traçabilité des stocks en rayonnage
L'efficacité d'un système de stockage moderne repose en grande partie sur sa capacité à intégrer des technologies de gestion informatisée. Ces outils permettent non seulement d'optimiser l'utilisation de l'espace, mais aussi d'assurer une traçabilité précise des stocks.
Systèmes WMS pour l'optimisation de l'entreposage
Les Warehouse Management Systems (WMS) ou systèmes de gestion d'entrepôt sont devenus indispensables pour gérer efficacement les opérations de stockage complexes. Ces logiciels sophistiqués permettent d'optimiser l'allocation des emplacements, de guider les opérateurs dans leurs tâches et de générer des rapports détaillés sur les performances de l'entrepôt.
Un WMS performant peut réduire les erreurs de préparation de commandes de plus de 70% et améliorer l'utilisation de l'espace de stockage de 10 à 20%. L'intégration d'algorithmes d'intelligence artificielle dans les WMS les plus avancés permet même de prédire les pics d'activité et d'ajuster dynamiquement les stratégies de stockage.
Technologie RFID appliquée au suivi des emplacements
La technologie d'identification par radiofréquence (RFID) révolutionne la traçabilité des stocks en rayonnage. En équipant les palettes et les emplacements de stockage de puces RFID, il devient possible de suivre en temps réel la localisation exacte de chaque unité de stockage.
L'implémentation de la RFID dans les entrepôts peut réduire les erreurs d'inventaire de plus de 95% et accélérer les processus de réception et d'expédition de 30 à 50%. Cette technologie s'avère particulièrement précieuse pour les industries soumises à des réglementations strictes en matière de traçabilité, comme l'industrie pharmaceutique ou agroalimentaire.
Interfaces avec les ERP pour une gestion intégrée
L'intégration des systèmes de gestion d'entrepôt avec les ERP (Enterprise Resource Planning) de l'entreprise permet une synchronisation en temps réel des données de stock avec les autres fonctions de l'entreprise. Cette interconnexion facilite la planification de la production, l'approvisionnement et la gestion des commandes clients.
Des études récentes montrent que les entreprises ayant mis en place une intégration complète entre leur WMS et leur ERP constatent une amélioration de la précision des prévisions de stock de l'ordre de 30%, ce qui se traduit par une réduction significative des ruptures de stock et des surstocks.
Maintenance préventive et sécurité des installations de stockage
La pérennité et la sécurité des systèmes de rayonnage industriels reposent sur une approche proactive de la maintenance. Une stratégie de maintenance préventive bien conçue permet non seulement de prolonger la durée de vie des installations, mais aussi de prévenir les accidents potentiellement graves.
Protocoles d'inspection et de vérification périodique
La mise en place de protocoles d'inspection réguliers est cruciale pour identifier précocement les signes d'usure ou de dommage sur les structures de rayonnage. Ces inspections doivent être menées selon un calendrier strict, avec une fréquence adaptée à l'intensité d'utilisation des installations.
Les inspections visuelles quotidiennes par les opérateurs, combinées à des contrôles approfondis trimestriels ou semestriels par des techniciens qualifiés, constituent la base d'un programme de maintenance efficace. Des outils numériques de gestion de la maintenance assistée par ordinateur (GMAO) peuvent être utilisés pour planifier et documenter ces inspections, assurant ainsi une traçabilité complète.
Techniques de réparation et renforcement des structures
Lorsque des dommages sont identifiés, il est essentiel d'intervenir rapidement avec des techniques de réparation appropriées. Les méthodes de renforcement varient en fonction de la nature et de l'étendue des dégâts, allant du simple remplacement de composants endommagés à des interventions plus complexes de renforcement structurel.
L'utilisation de techniques innovantes comme le renforcement par fibres de carbone pour les poutres endommagées ou l'application de revêtements spéciaux pour prévenir la corrosion peut significativement prolonger la durée de vie des installations. Des études de cas ont montré que ces techniques peuvent augmenter la résistance des structures de 15 à 25% tout en réduisant les coûts de remplacement.
Formation du personnel aux bonnes pratiques d'utilisation
La formation du personnel est un élément crucial pour garantir la sécurité et l'efficacité des opérations de stockage. Un programme de formation complet doit couvrir non seulement les aspects techniques de l'utilisation des rayonnages, mais aussi les procédures de sécurité et les bonnes pratiques de manutention.
Les opérateurs doivent être formés à reconnaître les signes de fatigue structurelle et à signaler immédiatement toute anomalie. Des sessions de formation régulières, combinant théorie et pratique, permettent de maintenir un niveau élevé de vigilance et de compétence. Des statistiques montrent que les entreprises investissant dans la formation continue de leur personnel connaissent une réduction des incidents liés au stockage de l'ordre de 40%.